Как развивается цементная промышленность России? Какие проблемы назрели внутри отрасли? Можно ли на основе опыта технологической модернизации в США и ЕС определить перечень необходимых мероприятий для перевода данной отрасли с энергоемкого (мокрого) способа производства на экономный (сухой)?
1. Краткая история развития отрасли. Цементная отрасль наряду с лесной и деревообрабатывающей, химической промышленностью, черной и цветной металлургией образует комплекс конструкционных материалов (ККМ), влияющий на экономический потенциал и уровень промышленного развития страны. Все отрасли ККМ относятся к отраслям по производству промежуточной продукции, т.е. основная часть продукции отрасли направляется на переработку в другие сектора экономики при относительно небольшой доле выпуска, приходящейся на конечное потребление.
Цементная промышленность России характеризуется как отрасль с высоким уровнем физического и морального износа производственных мощностей (износ активной части основных фондов превысил 70%), с низким технологическим уровнем развития, а, следовательно, и низкими показателями экологической безопасности производства. Во многом данная ситуация обусловлена историей развития данной отрасли промышленности в постсоветское время [19]:
- 1989-1991 гг. – потеря управления, начало экономических реформ и спада производства, приватизация как попытка решения основной задачи экономической реформы – создание класса эффективных собственников.
- 1991-1992 гг. – резкое снижение объемов строительства, падение спроса на цемент, тяжелая адаптация цементных заводов к условиям рыночной экономики.
- 1992-1998 гг. – кризисные явления трансформации плановой экономики в рыночную. Этот период характеризуется снижением производства цемента более чем в 3 раза с 84.7 до 26.0 млн. тонн, выбытием 19 млн. тонн мощностей, существенным сокращением отраслевой науки, приходом на российский рынок зарубежных компаний «Holderbank» (Holcim), «Dyckerhoff», «Lafarge». По данным Росстата в этот период до 40% цементных заводов были убыточными. На основе московских перевалочных терминалов консолидируется крупнейшая цементная компании РФ – ОАО «Штернцемент».
- 1999-2001 гг. – начало подъема экономики и как следствие увеличение спроса на цемент. Первые успешные попытки крупных игроков влиять на ценообразование на рынке. Формируется высокая инвестиционная привлекательность цементной отрасли. Ведется активная скупка акций цементных заводов российскими и зарубежными компаниями.
- 2002-2005 гг. – период крупных M&A сделок. Росуглесбыт поглощает ОАО «Штернцемент» с дальнейшим переименованием в Евроцемент. Компания ИНТЕКО, начав с приобретения двух заводов, доводит их количество в группе до пяти. На рынке наблюдается интенсивный рост производства цемента на 8-12% в год, сопровождающийся ценовой войной между ключевыми участниками рынка.
- Апрель 2005 г. – формирование монопольного игрока на рынке цемента Европейской части РФ (Сделка Евроцемент-ИНТЕКО и Евроцемент-Су-155). Евроцемент контролирует более 40% российского рынка цемента. Вмешательство ФАС в регулирование показателей цены и объемов производства носит скорее демонстративный характер.
- 2005-2007 гг. – темпы роста производства цемента продолжают оставаться высокими. Цены на цемент, объемы производства, инвестиционная привлекательность цементного бизнеса достигают максимальных уровней. Появляются признаки дефицита цемента и тенденция к увеличению объемов импорта. Использование мощностей на многих предприятиях Европейской части РФ приблизилось к своему пределу.
По объемам производства в условиях постоянного роста спроса за период 2000-2007 гг. Россия достигла уровня 72% от объема выпуска 1990 года.
В докризисный период основными локомотивами роста спроса на цемент являлись федеральные целевые программы (ФЦП) “Доступное жилье”, “Сочи 2014” и др. Национальные программы, реализуемые в РФ, являются весьма емкими по объему вовлекаемых ресурсов, в том числе и в рамках продукции промышленности строительных материалов, строительного сектора.
Ожидалось, что среднегодовой темп прироста потребности экономики России в цементе до 2015 г. будет не менее 10%. По экспертным оценкам НИИцемента, датированным 2007 годом, потребность стройкомплекса в цементе в 2010 г. могла составить 80-90 млн. т, а в 2012-2015 гг. – 115-120 млн. т. При дальнейшем снижении темпов прироста до 8% в 2016 г. и до 5% в последующие годы потребность выросла бы до 125-127 млн. т, в 2020 г. – до 150-162 млн.т. и в 2025 г. – до 190-206 млн. т.
В докризисный период спрос на данную продукцию отрасли опережал предложение, что приводило к увеличению цен на внутреннем рынке, созданию условий для импорта цемента из Европы, Китая, Турции и других стран.
Следует учитывать, что спрос на цемент носит сезонный характер, зависящий как от спроса со стороны основных его секторов-потребителей, так и применяемых технологий для его производства. Устаревшие технологии производства не позволяют в отдельных случаях производить клинкер в зимний период, что формирует дисбаланс в месячной загрузке на отдельных производствах, напрямую влияет на уровень использования производственных мощностей, привлечение инвестиций в отрасль, загрузку транспортного парка для перевозки цемента (табл.1) [1].
![]() |
![]() |
![]() |
![]() |
![]() |
![]() |
![]() |
![]() |
![]() |
![]() |
![]() |
![]() |
![]() |
|
---|---|---|---|---|---|---|---|---|---|---|---|---|---|
2010 | 1,70 | 2,10 | 3,20 | 4,00 | 4,90 | 5,60 | 5,60 | 5,90 | 5,30 | 5,10 | - | - | - |
2009 | 1,63 | 2,42 | 3,00 | 3,49 | 4,08 | 4,64 | 5,16 | 4,90 | 4,80 | 4,30 | 3,00 | 2,80 | 44,22 |
2008 | 2,95 | 3,68 | 4,62 | 5,37 | 5,38 | 5,09 | 5,53 | 5,40 | 5.02 | 4,62 | 3,21 | 2,58 | 53,48 |
2007 | 6,04 | 3,49 | 4,37 | 5,23 | 5,62 | 5,87 | 6.01 | 6,09 | 5,96 | 5,78 | 4,58 | 3.45 | 59,66 |
2006 | 2,06 | 2,30 | 3,64 | 4,44 | 5,02 | 5,41 | 5,97 | 5,93 | 5,44 | 5,31 | 4,57 | 4,02 | 54,73 |
2005 | 2,07 | 2,39 | 3,15 | 3,64 | 4,10 | 5,05 | 5,34 | 5,53 | 5,10 | 4,94 | 3,64 | 3,23 | 48,35 |
2004 | 2,00 | 2,40 | 3,20 | 3,80 | 4,30 | 4,80 | 5,00 | 5,00 | 4,70 | 4,40 | 3,40 | 2,60 | 45,61 |
2003 | 1,60 | 2,10 | 2,70 | 3,30 | 3,80 | 4,30 | 4,70 | 4,70 | 4,30 | 4,10 | 3,20 | 2,30 | 40,99 |
2000 | 1,70 | 1,80 | 2,20 | 2,50 | 2,80 | 3,20 | 3,30 | 3,60 | 3,30 | 3,20 | 2,80 | 2,10 | 32,28 |
2. Развитие отрасли в кризисный период. Первым годом развития отрасли в условиях кризиса является 2008 г. Наибольший спад объемов производства в 2008 году к аналогичным месяцам в 2007 году приходится на январь (в 2 раза). В остальные месяцы – на 15-20% по отношению к аналогичным периодам. Спад объясняется как ростом цен на энергоносители, так и снижением объемов строительства жилья.
Другой составляющей, оказавшей влияние на объемы производства цемента, явилось принятие мер по регулированию импортных поставок данной продукции. После отмены таможенных пошлин на импорт цемента ведущие холдинги данного сектора экономики, на долю которых приходится более 70% всех производственных мощностей (ЗАО “ЕВРОЦЕМЕНТ-груп”, “Холсим” и “Сибирский цемент”), для удержания отпускных цен стали сокращать объемы его производства, создавая тем самым “искусственный дефицит” (8,8 млн. т цемента), который впоследствии был компенсирован за счет внешних поставок.
Итогом данных мероприятий явилось сокращение объема производства цемента в 2008 г. по сравнению с 2007 г. на 10,6% (53,48 млн. т). В 2009 г. динамика сокращения выпуска сохранилась (с 53,48 до 44,1 млн. т).
Падение спроса на жилье вследствие снижения платежеспособности населения, рост цен на энергоносители (электроэнергию, природный газ, уголь) нашло прямое отражение на объемах внутреннего потребления цемента, объемах его производства: за январь-июль в 2009 году отрасль достигла аналогичных объемов 2003 года. Наибольший спад объемов производства в 2009 году к аналогичным месяцам в 2008 году приходится на январь (почти в 2 раза). С февраля по июль – 15-20%, в остальные месяцы – 5-7% по отношению к аналогичным периодам.
Объем производства цемента в 2009 г. составил 96,7% от выпуска 2004 г. Отчетный период можно охарактеризовать как переломный: за первые шесть месяцев 2010 г. было произведено 21,5 млн. т цемента, что на 11,6% больше аналогичного показателя за 2009 г.
Максимальные объемы производства цемента в 2010 г. достигнут уровня 49-51 млн. т, т.е. уровня 2005-2006 годов.
Перспективные объемы производства цемента зависят от скорости восстановления объемов строительства жилья.
По экспертным оценкам, за 2010-2011 гг. будет введено около 110 млн. кв. м жилой площади (110-120 млн. т цемента), что фактически может быть покрыто за счет существующих производственных мощностей цементной промышленности.
Исходя из вышеизложенного, перспективы развития отрасли определяются такими ключевыми факторами как: используемые технологии, спрос на продукцию, инвестиции и транспортная инфраструктура.
3. Технологическое развитие отрасли. Производство цемента состоит из двух технологических циклов: 1. производство клинкера; 2. измельчение клинкера совместно с гипсом и другими добавками – получение портландцемента. В зависимости от способа подготовки сырьевых смесей различают сухой, мокрый и комбинированный способы производства клинкера.
При мокром способе тонкое измельчение сырьевой смеси производят в водной среде с получением шихты в виде водной суспензии – шлама 30-50%. В настоящее время в России мокрым способом производится около 85% клинкера.
При сухом способе производства сырьевую шихту готовят в виде тонкоизмельченного сухого порошка, поэтому перед помолом или в процессе его сырьевые материалы высушивают. Данный способ нашел наибольшее распространение в мире, поскольку является менее энергоёмким по сравнению с мокрым способом.
Комбинированный способ может базироваться как на мокром, так и на сухом способе производства шихты. В первом случае сырьевую смесь готовят по мокрому способу в виде шлама, обезвоживают на фильтрах и подают на обжиг в печи в виде полусухой массы. Во втором случае сырьевую смесь готовят по сухому способу, а затем гранулируют с добавкой воды, после чего происходит обжиг.
Одной из основных проблем отрасли является несовершенство технологического процесса, поскольку российский цемент производится по высокозатратным, устаревшим технологиям.
Почти 85% клинкера в отечественной цементной промышленности производится мокрым способом производства с удельным расходом условного топлива до 200-230 кг.у.т./т, в то время как в промышленно-развитых странах (Япония, ЕС) большая часть клинкера обжигается по сухому способу с расходом 120-130 кг.у.т./т., а в отдельных случаях – 100 кг.у.т./т. В США 80% мощностей ориентированы на сухой способ производства, 20% – на мокрый.
Процесс перехода США с мокрого на сухой способ производства цемента составил около 25 лет: доля мощностей, работающих по технологии сухого производства, была увеличена с 38% до 80% [3-17]. Изменение пропорций производства цемента в США сухим, мокрым и комбинированным способами представлено на рис.1.
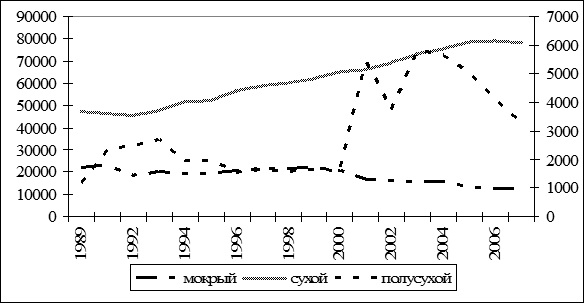
Рис.1. Изменение пропорций производства цемента в США сухим, мокрым, комбинированным способами с 1990 по 2008 гг.
Печной парк цементной промышленности США по состоянию на 01.01.2007 состоит из 54 печей мокрого способа и 132 – сухого способа производства (табл.2) [2].
Типы печей | Число печей | Доля мощностей |
---|---|---|
Мокрые печи | 54 | 15-20% |
Сухие длинные | 52 | 15-20% |
Сухие с циклонами | 80 | 50-60% |
Итого США | 186 | 100% |
Технологическая структура производства цемента в других странах-производителях представлена в табл.3 [2].
Страна | Технологии производства клинкера (% от объема производства (выпуска)) | |||
---|---|---|---|---|
Сухой | Полусухой | Мокрый | Старые шахтные печи | |
ЕС | 90 | 7,5 | 2,5 | |
Китай | 50 | 0 | 3 | 47 |
Индия | 50 | 9 | 25 | 16 |
США |
82 |
0 |
18 |
0 |
Япония | 100 | |||
Россия |
12 |
3 |
78 |
7 |
Испания | 92 | 4,5 | 3,5 | 0 |
Мексика | 67 | 9 | 23 | 1 |
Проводя модернизацию цементной промышленности, Россия первоначально должна приблизиться к структуре США. Только 2 из 190 действующих в России печных агрегатов могут быть отнесены к числу современных (ОПО “Невьянский цементник” (Свердловская область) и ОАО “Серебряков цемент” (Волгоградская область)). Технологическая структура печного парка цементной промышленности России представлена в табл.4 [2].
Типы печей | Доля печей, % | Доля мощностей, % |
---|---|---|
Мокрые печи (короткие) | 33 | 26 |
Мокрые печи (длинные) | 52 | 57 |
Сухие | 9 | 17 |
Шахтные | 6 | |
Итого РФ | 100 | 100 |
Российские заводы, работающие по сухому способу, в основном, используют устаревшие технологии, что не дает экономии в затратах, типичной для этого способа производства в других странах.
Почти весь цемент и до 90% сырья в отечественной промышленности измельчается в шаровых мельницах открытого цикла помола. Расход электроэнергии только на передел помола цемента составляет около 40 кВт*ч, в то время как при широко распространенном за рубежом замкнутом цикле он не превышает 25-30 кВт*ч.
Кроме того, использование в системах замкнутого цикла высокоэффективных сепараторов 3-го поколения позволяет направленно влиять на гранулометрический состав цемента и обеспечивать получение заданных свойств, в том числе при производстве многокомпонентных цементов. Расход топлива на этих агрегатах составляет соответственно 128 и 143 кг.у.т./т клинкера, т.е. находится на уровне 60-65% от среднеотраслевого уровня затрат и соответствует уровню расхода в ЕС (табл.5) [18].
Процесс (способ) | Удельное потребление (кг.у.т/т) |
---|---|
Сухой способ, многостадийный (от трех до шести), циклонные теплообменники и печи декарбонизации | 102,4-136,5 |
Роторные печи сухого способа с циклонными теплообменниками | 105,8-143,3 |
Комбинированный полусухой-полумокрый способ | 112,6-184,3 |
Сухой способ – длинные печи | До 170,6 |
Мокрый способ – длинные печи | 170,6-210 |
Шахтные печи и производство особых видов цементов | 105-221,8 и выше |
Однако переход на сухой способ производства в России влечет за собой определенные проблемы. Если цена тонны условного топлива у нас в стране повысится до уровня западной, то не менее 80% цемента Россия вынуждена будет производить по сухому способу производства или же вообще прекратить его производство. Дешевле станет покупать его в Турции, Китае и других странах. Энергоемкий мокрый способ производства станет неконкурентоспособным по сравнению с сухим, являющимся более дешевым. На коренную же реконструкцию и модернизацию требуются достаточно большие вливания инвестиций в данный сектор экономики. Так, в частности, на перевод завода мощностью в 1 млн. т на сухой способ производства требуется около 70 млн. долларов США.
Поэтому в условиях технологической реструктуризации данной отрасли необходимо проведение мероприятий по поэтапному переводу мощностей на сухой способ производства, проявляющееся как в реконструкции действующих линий, так и строительстве новых цементных заводов. Использование помола сырья в замкнутом цикле, позволяющего снизить энергоемкость процесса в 1,5 раза (с 40 до 25 кВт*ч), а также снижение влажности шлама за счет применения новых более эффективных разжижителей, позволяющих сократить на 15-20% удельный расход топлива, дают возможность приблизить (по затратам топливно-энергетических ресурсов) мокрый способ производства к сухому, обеспечивая его конкурентоспособность.
Удешевление затрат на топливно-энергетические ресурсы возможно также посредством использования альтернативных источников.
В мировой практике используют различные подходы к выбору топливно-энергетических ресурсов, используемых при производстве клинкера. К основным топливно-энергетическим ресурсам можно отнести природный газ, уголь, мазут, сланцы. Наряду с ними широкое применение находит внедрение альтернативных видов топлива, позволяющее решать одновременно две задачи – утилизацию вторичного сырья и замену основного ресурса (природного газа, угля, мазута).
В странах ЕС в составе технологического топлива, используемого при производстве цемента, все в большей степени находят применение вторичные виды ресурсов. Замещение основного вида топлива вторичным в отдельных странах ЕС составило: во Франции – 27%, в Австрии – 29%, в Швейцарии – 34%, в Нидераландах – 72%.
В качестве альтернативного топлива используются топливо-содержащие отходы – шины, резина, отработанные масла, пластик, бумага, переработанные фракции из бытовых отходов, животной муки и жиров, древесины, растворителей и т.п.
Доля энергоносителей в себестоимости цемента, производимого в РФ, составляет 50-57%. Распределение топлива, используемого при производстве цемента, представлено в табл.5 (% от объёма использованных топливно-энергетических ресурсов) [1].
Вид топлива | 2000 | 2001 | 2002 | 2004 | 2006 | 2008 | 2009 |
---|---|---|---|---|---|---|---|
Природный газ | 86.8 | 90.7 | 91.7 | 93.2 | 92.4 | 92.1 | 91,9 |
Мазут | 4.7 | 2.2 | 2.3 | 1.5 | 1.5 | 1.9 | 2,2 |
Уголь | 8 | 6.5 | 5.4 | 5 | 6.1 | 6 | 6,9 |
Сланец | 0.5 | 0.6 | 0.6 | 0.3 | 0 | 0 | 0 |
Ориентация отрасли на один топливно-энергетический ресурс делает ее “уязвимой” к динамике цен на него. Опережающий рост цен на топливно-энергетические ресурсы по сравнению с ценами на цемент приводит к увеличению себестоимости продукции данной отрасли, а в условиях стабилизации цен на него – снижению финансовых показателей, влияющих на объем привлекаемых инвестиций, определяющих процесс модернизации цементной промышленности, её технологическое развитие.
Наглядно это может быть проиллюстрировано на основании данных базовых индексов цен на промышленную продукцию за период 1995-2009 гг. (табл.6) [1].
1996 | 1997 | 1998 | 1999 | 2000 | 2001 | 2002 | 2003 | |
---|---|---|---|---|---|---|---|---|
Электроэнергия | 100.0 | 108.50 | 110.89 | 132.73 | 188.08 | 242.25 | 310.80 | 325.50 |
Топливо дизельное | 100.0 | 121.00 | 130.20 | 419.88 | 646.62 | 602.00 | 627.89 | 797.40 |
Мазут топочный | 100.0 | 116.00 | 123.19 | 316.85 | 594.09 | 380.22 | 591.24 | 578.80 |
Газ естественный | 100.0 | 100.60 | 109.25 | 124.11 | 201.06 | 307.82 | 417.40 | 295.10 |
Уголь | 100.0 | 99.40 | 98.90 | 122.24 | 171.26 | 212.02 | 237.89 | 242.40 |
Цемент | 100.0 | 107.90 | 114.37 | 151.89 | 227.23 | 282.90 | 343.44 | 437.50 |
2004 | 2005 | 2006 | 2007 | 2008 | 2009 | |
---|---|---|---|---|---|---|
Электроэнергия | 392.6 | 435.8 | 480.7 | 548.5 | 650.19 | 737.7 |
Топливо дизельное | 1275.1 | 1505.9 | 1454.7 | 1899.8 | 1238,7 | 1397.9 |
Мазут топочный | 548.7 | 1139.2 | 1154.0 | 1879.8 | 979,38 | 1527.7 |
Газ естественный | 624.1 | 740.2 | 840.2 | 961.2 | 1183,6 | 1141.0 |
Уголь | 347.9 | 415.7 | 397.8 | 463.1 | 630.0 | 562.59 |
Цемент | 500.5 | 590.6 | 745.4 | 1233.6 | 969.24 | 798.36 |
Данные табл.6 показывают, что на всем анализируемом периоде цены на газ росли быстрее цен на цемент, исключением является 2003 г.; аналогичная ситуация и с продуктами нефтепереработки (топливо дизельное, мазут топочный). Уголь является наиболее предпочтительным топливно-энергетическим ресурсом. Ограничениями на перевод производственных мощностей на уголь являются: 1. транспортные издержки на его доставку потребителю; 2. необходимость установки нового оборудования, работающего на нем (в настоящее время в РФ не используются технологии ориентированные на комбинированный вариант – уголь+природный газ); 3. Использование определенных марок угля (марки, группы, подгруппы бурых углей и антрацитов Д, ДГ, СС, ТС, Т и не использующиеся для коксования Г, ГЖО,КС, КСН).
4. Транспортная инфраструктура отрасли. Цемент является сыпучим продуктом и перевозится всеми видами транспорта. Ключевая роль в данном направлении принадлежит железнодорожному транспорту (табл.7) [1], на долю которого приходится более 85% перевозок (рис.2).
1991 | 1995 | 2000 | 2005 | 2006 | 2007 | 2008 | |
---|---|---|---|---|---|---|---|
Всего | 70,43 | 32,10 | 27,43 | 42,25 | 47,53 | 53,55 | - |
Ж/Д | 63,00 | 26,80 | 22,40 | 34,30 | 38,30 | 41,90 | 36,0 |
Морской транспорт | 0,58 | 0,20 | 0,20 | 0,05 | 0,08 | 0,08 | н/д |
Внутренний водный | 0,70 | 0,13 | 0,05 | 0,13 | 0,08 | 0,33 | н/д |
Прочие виды транспорта | 6,18 | 5,00 | 4,80 | 7,78 | 9,10 | 11,28 | н/д |
Средняя дальность перевозок на ж/д транспорте, км | |||||||
н/д | 503 | 528 | 603 | 645 | 738 | 1143 |
За анализируемый период средняя дальность перевозок увеличилась в 2 раза, что, в частности, отражает географию потребителей данной продукции – крупные города, мегаполисы, в которых строительный сектор снизил объемы строительства, но не остановился; развитие сектора жилищного строительства происходит по большей части за счет реализации проектов, сформированных еще в докризисный период и находящихся в стадии завершения. (Справочно: средняя дальность перевозок цемента в странах Евросоюза составляет менее 250 км.)
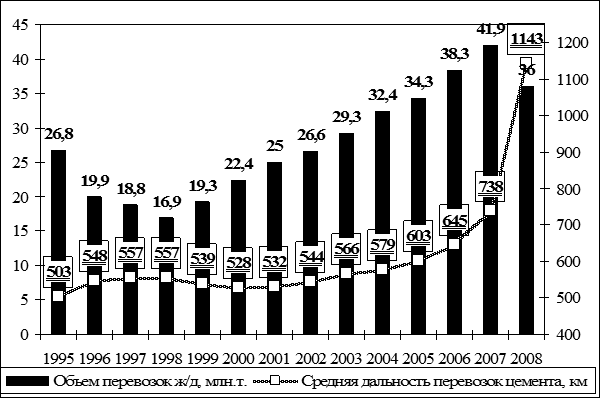
Рис.2. Средняя дальность и объемы перевозок цемента ж/д транспортом.
Достижение данного показателя возможно посредством формирования “зональных” перевозок, ориентированных на доставку продукции потребителю внутри субъекта РФ. Все это требует развития не только Федеральных целевых программ, выполняемых преимущественно в региональных центрах, но и ориентированных на снижение доли аварийного/ветхого жилого фонда в крупных и средних муниципальных образованиях субъекта РФ, где строительный сектор ориентирован преимущество на развитие многоэтажного строительства. Одним из сдерживающих факторов в выполнении данного направления является фактор неравномерного расположения минерально-сырьевой базы отрасли, определяющей географию развития/размещения предприятий цементной промышленности.
Объемы перевозок цемента на железнодорожном транспорте зависят как от пропускной способности, так и подвижного состава, его качества. Цемент перевозится в хоппер-вагонах: срок эксплуатации большей части их фонда составляет более 20 лет, прошедших не один раз капитальный ремонт. При устойчивом росте внутреннего потребления на цемент в 2000-2007 гг. фиксировалась нехватка тоннажа как для перевозки цемента от отечественных производителей до потребителей, так и со стороны импортеров. Активный выпуск вагонов данного типа предприятиями машиностроительного комплекса позволил в короткие сроки провести обновление одной из неотъемлемой части фондов данной отрасли, но не решить саму проблему в целом. Из-за дефицита хоппер-вагонов в 2007 г. не было вывезено с российских цементных заводов несколько млн. т произведенного цемента. В дальнейшем, после прохождения периода стагнации на рынке цемента и роста внутреннего потребления на цемент, аналогичная ситуация может повториться.
В докризисный период, в условиях опережения предложения над спросом, компенсация дефицита на рынке происходила посредством импорта цемента как из стран СНГ, в первую очередь, с Украины и из Белоруссии, так и вне СНГ – Турции и Китая. Если со стороны стран СНГ цемент доставляется преимущественно ж/д транспортом, то из Китая и Турции – морским. Эти страны близко расположены к основным перевалочным пунктам: черноморским (Новороссийск) и дальневосточным (Находка, Владивосток) морским портам. Цемент там значительно дешевле, чем у нас: в Турции — около 100 долларов за тонну, в Китае — около 50–60 долларов (по состоянию на 01.07.2010).
Российские порты не могут принимать цемент навалом (то есть засыпать его с судов в железнодорожные вагоны), так как отсутствуют специальные терминалы. По этой причине морские поставки осуществляются в специальных мешках — биг-бэгах емкостью полторы-две тонны. Перевалочные работы из биг-бэгов являются трудоемкими и высокозатратными, учитывая отсутствие отлаженной механизированной перегрузки, т.е. фактически грузы обрабатываются вручную.
В полувагоне умещается 60–70 таких мешков. Поскольку вагоны металлические, то существует риск разрыва биг-бэгов, а значит и уровень потерь цемента с 1 импортируемой тонны морским транспортом возрастает в разы по отношению к требованиям, используемым при составлении финансовой отчетности – норм естественной убыли (НЕУ) при транспортировке и погрузочно-разгрузочных работах (ПРР).
Комплексные потери при транспортировке и разгрузке цемента в биг-бэгах доходят до 5–10% против 0,25% при самой транспортировке и 1-2% при ПРР.
По экспертным оценкам, страны-экспортеры способны производить для России не менее 10–12 млн. тонн цемента в год. Флот в состоянии осуществлять транспортировку таких объемов цемента, а инфраструктура портов позволяет ежегодно принимать не более 7–8 млн. тонн цемента в год.
“Ахиллесовой пятой” морских портов остается железнодорожная инфраструктура, перегруженная и работающая на пределе своих возможностей. Китай в случае сворачивания/переноса на неопределенный срок инвестиционных программ по вводу производственных мощностей в РФ может занять первое место среди стран-импортеров цемента в нашу страну.
Неразвитость логистической инфраструктуры портов Дальнего Востока оказывает существенное влияние на объемы их поставок – максимально не более 400 тыс. тонн в год.
Другой аспект связан с качеством получаемой конечным потребителем продукции: если цемент пролежал на хранении месяц, то он теряет одну единицу в марочности. Таким образом, купив в Китае марку 500ДО, московские потребители, до которых цемент идет в лучшем случае месяц, рискуют получить марку 400ДО.
Все это требует пересмотра подходов к формированию транспортно-логистических коридоров и инвестиций в развитие транспортной инфраструктуры морских портов.
5. Спрос на продукцию. Интенсивность потребления цемента в регионах зависит от объемов строительства жилого и производственного фонда, дорог специального назначения, транспортной и торгово-посреднической наценки на цемент, скорости его доставки, определяющей удаленность потребителя от поставщика (завода). Возникновение профицита/дефицита цемента во внутреннем потреблении на уровне регионов должно рассматриваться как один из ключевых факторов развития производственной структуры данной отрасли в регионах и федеральных округах (табл.8) [1].
Федеральные округа | Производство | Потребление | ||||
---|---|---|---|---|---|---|
2006 | 2007 | 2008 | 2006 | 2007 | 2008 | |
Центральный | 54,73 | 59,93 | 53,48 | 53,25 | 61,07 | 60,93 |
Северо-Западный | 15,38 | 15,31 | 11,42 | 18,47 | 19,99 | 16,83 |
Южный | 3 ,45 | 4,34 | 3,37 | 3,86 | 4,29 | 4,28 |
Приволжский | 9,62 | 9,93 | 9,86 | 7,77 | 8,96 | 7,88 |
Уральский | 6,23 | 6,63 | 5,78 | 5,17 | 6,20 | 6,40 |
Сибирский | 7,07 | 8,53 | 8,99 | 6,06 | 7,35 | 6,35 |
Дальневосточный | 1,42 | 2,01 | 2,92 | 1,43 | 1,54 | 1,62 |
Импорт | 0,79 | 2,75 | 8,13 | |||
Экспорт | 3,20 | 1,86 | 0,80 |
Анализ производства и потребления цемента по федеральным округам показывает, что завозным регионом является ЦФО и вывозными – Южный и Приволжский федеральные округа, поэтому и производственные мощности должны располагаться на минимальном удалении от их основных потребителей для минимизации транспортных и других затрат, влияющих на цену конечного потребителя.
Организация межрегиональных поставок зависит не только от наличия транспорта и подвижного состава, существующих логистических коридоров для осуществления поставок, но и от объемов внутреннего потребления в регионах, где расположены сами производства. В данном случае нельзя не учитывать и нюанс приграничного расположения заводов, ориентирующих их на формирование направления поставок, в том числе и в близлежащие регионы (табл.9). Исходя из данных табл.9, можно сделать выводы о наличии или отсутствии возможностей цементных заводов покрывать внутренний спрос и целесообразности развития дополнительных производственных мощностей в регионах.
Завод | Потребление цемента в регионе его производства, млн. т. | Доля |
---|---|---|
Евроцемент | 14,29 | 93% |
Белгородский цемент | 1,41 | 95% |
Жигулевские стройматериалы | 0,53 | 93% |
Кавказцемент | 1,95 | 96% |
Катавский цемент | 0,38 | 78% |
Липецкцемент | 0,95 | 92% |
Мальцовский портландцемент | 2,16 | 94% |
Михайловцемент | 1,18 | 99% |
Невьянский ЦЗ | 0,77 | 92% |
Осколцемент | 2,16 | 91% |
Пикалевский ЦЗ | 1,24 | 99% |
Подгоренский цементник | 0,09 | 55% |
Савинский цемзавод | 0,52 | 92% |
Ульяновскцемент | 0,91 | 86% |
Завод | Потребление цемента в регионе его производства, млн. т. | Доля |
---|---|---|
Сибирский цемент | 3,90 | 78% |
Ангарскцемент | 0,83 | 85% |
Каменский ЦЗ (Тимлюйцемент) | 0,40 | 96% |
Красноярский ЦЗ | 0,92 | 100% |
Топкинский цемент | 1,74 | 65% |
Новоросцемент | 3,26 | 81% |
Новоросцемент | 3,26 | 81% |
Мордовцемент | 2,00 | 55% |
Мордовцемент | 2,00 | 55% |
Себряковцемент | 1,97 | 59% |
Себряковцемент | 1,97 | 59% |
Lafarge | 2,86 | 87% |
Воскресенскцемент | 1,81 | 100% |
Уралцемент | 1,06 | 71% |
Holcim | 2,11 | 68% |
Вольскцемент | 1,23 | 56% |
Щуровский цемент | 0,88 | 98% |
Полное использование мощностей цементных заводов для покрытия внутреннего спроса в субъектах РФ их нахождения продуцирует ввоз цемента из других, в свою очередь, увеличивая среднюю дальность перевозки этой продукции до потребителя и рост транспортной составляющей в конечной его стоимости.
Отсутствие ввода новых, рост уровня износа фондов (ОПФ) привели к сокращению мощностей на 15-18 млн. т. Ежегодное выбытие производственных мощностей составляет около 1,2-1,5 млн. т. Износ производственных фондов достиг уровня 70%.
Мощность цементных заводов России по состоянию на 01.01.2008 составила 76 млн. т, уровень загрузки – 65-70%. Данного фонда мощностей достаточно для покрытия спроса на внутреннем рынке в объеме 60 млн. т. По оптимистичному сценарию, производственные мощности отрасли к 2015 г. возрастут до 100 млн. т, к 2020 г. – до 125-140 млн. т.
Таким образом, ввод в эксплуатацию мощностей по производству цемента может составить ежегодно, начиная с 2012 г., от 4 до 7 млн. т. Фактически будет введено 50-60 млн. т производственных мощностей, работающих по сухому способу производства. Одновременно с вводом производственных мощностей необходимо проведение ежегодной реконструкции технологических линий мокрого способа производства мощностью в 2-3 млн. т, ориентированных на комбинированный вариант использования топливно-энергетических ресурсов (уголь и мазут; газ и мазут, сланцы).
6. Выводы и предложение. Цементная промышленность является ключевой отраслью комплекса конструкционных материалов. В условиях отсутствия финансирования на реконструкцию и развитие данного сектора экономики его производственные мощности сократились на 15-18 млн. т и составили 70 млн. т, а уровень их износа до 75%. При таких условиях максимальные (пиковые) объемы производства цемента составляют 55-60 млн. т.
Развитие федеральных программ, требующих привлечения большого количества ресурсов, в том числе и продукции данной отрасли, нашли свое отражение в росте импорта цемента, преимущественно из стран СНГ (Украины, Белоруссии): с 2000 по 2007 гг. импорт цемента увеличился с 0,1 до 2,4 млн. т. В докризисный период объемы производства цемента достигли уровня 71% от объема производства в 1990 г. и выросли с 2000 по 2007 гг. с 35,3 до 59,7 млн. т, т.е. на 24,4 млн. т.
Правовое регулирование, направленное на снижение стоимости цемента для конечного потребителя, проявившееся в отмене таможенных пошлин на импортируемый цемент, привело к созданию “искусственного дефицита” со стороны российских производителей, сокративших объемы его производства на 8,8 млн. т в 2008 г. Аналогичная ситуация повторилась и в 2009 г.
Дальнейшее развитие отрасли определяется возможностями обновления и наращивания мощностей для покрытия внутреннего потребления за счет “цемента российских производителей”. Объем заявленного ввода/реконструкции мощностей в отрасли до 2015 г. холдингами составил 50% от имеющихся мощностей (около 35 млн. т).
До 85% цемента в отрасли производится мокрым способом, являющимся энергоемким, при котором затраты топливно-энергетических ресурсов превышают в 2 раза международные, где основным является сухой способ. Актуальным для РФ является использование опыта США по переводу с мокрого на сухой способ производства (процесс перевода мощностей США составил около 25 лет). Естественно, технологическое реформирование данного сектора не может быть ориентировано на данный срок. По нашему мнению, технологическая модернизация данного сектора должна составить около 10 лет, т.е. до 2020 г.
Снижение объемов жилищного строительства и цен на продукцию привело в большинстве случае к переносу большей части инвестиционных проектов на неопределенный срок. В лучшем случае проводятся подготовительные работы по формированию инфраструктуры, разработке карьеров для поставки сырья на завод, а также реконструкция действующих линий.
Все это при условии оживления строительной отрасли может сгенерировать рост импорта цемента, ограничениями на который является дефицит подвижного состава (хоппер-вагонов) и неразвитость инфраструктуры портов, через которые возможно наращивание поставок дешевого цемента, в первую очередь из Китая. Неравномерное расположение ключевых потребителей данной продукции приводит к росту дальности ее перевозок и сроков доставки конечному потребителю, что напрямую отражается на качестве цемента (его марочности). Одним из решений данного вопроса является налаживание операций реимпорта цемента из стран СНГ, закупающих его в Китае. Белоруссию в данном случае следует рассматривать как одну из основных стран-участниц этой модели внешних закупок. Логика модели реимпорта достаточно прозрачна: предприятия Белоруссии для формирования необходимых стабильных финансовых результатов импортируют его в РФ, а строительные организации Белоруссии, как основные потребители, решают вопрос его импорта из Китая. Частично такого рода модель поставок была реализована в 2006-2007 гг.
- Данные сайта ФСГС www.gks.ru.
- Данные НИЦ “Гипроцемент-наука”.
- USA Bureau of Mines/ Mineral yearbook 1990.
- USA Bureau of Mines/ Mineral yearbook 1992.
- USA Bureau of Mines/ Mineral yearbook 1994.
- USA Bureau of Mines/ Mineral yearbook 1996.
- USA Bureau of Mines/ Mineral yearbook 1994.
- USA Bureau of Mines/ Mineral yearbook 1996.
- USA Bureau of Mines/ Mineral yearbook 1994.
- USA Bureau of Mines/ Mineral yearbook 1996.
- USA Bureau of Mines/ Mineral yearbook 1996.
- USA Bureau of Mines/ Mineral yearbook 1998.
- USA Bureau of Mines/ Mineral yearbook 2000.
- USA Bureau of Mines/ Mineral yearbook 2002.
- USA Bureau of Mines/ Mineral yearbook 2004.
- USA Bureau of Mines/ Mineral yearbook 2006.
- USA Bureau of Mines/ Mineral yearbook 2008.
- Данные Европейской ассоциации производителей цемента (www.cembureaux.org).
- материалы ООО «СМПро».
Написать комментарий
Статья интересная. На сегодняшний день серьезным препятствием для развития цементной отрасли является транспортная проблема. В самом начале строительного сезона, по данным СМПРО, объем отгрузок цемента железнодорожным транспортом повысился на 43,3%. В марте он составил примерно 2,75 млн. тонн, а цена аренды вагонов с начала года подорожала на 10-15%. На сколько мне известно, новые цементные заводы активно решают проблемы логистики. Например, строящийся цементный завод в Чудовском районе - Бабиновский цемзавод - планирует диверсифицировать систему доставки цемента, он будет более активно работать с заказчиками своего региона, инвестирует средства в закупку цементовозов и организацию ж/д грузоперевозок
Материал заслуживает внимания, но по результатам цементной промышленности за 2010г требует существенной корректировки и ряд выводов по перспективе будут иными. Следует сделать акцент на приближение в ближайшие годы внутренних цен на топливо к общемировым, что отразится на рентабельности дальнейшей эксплуатации заводов по мокрому способу производства.